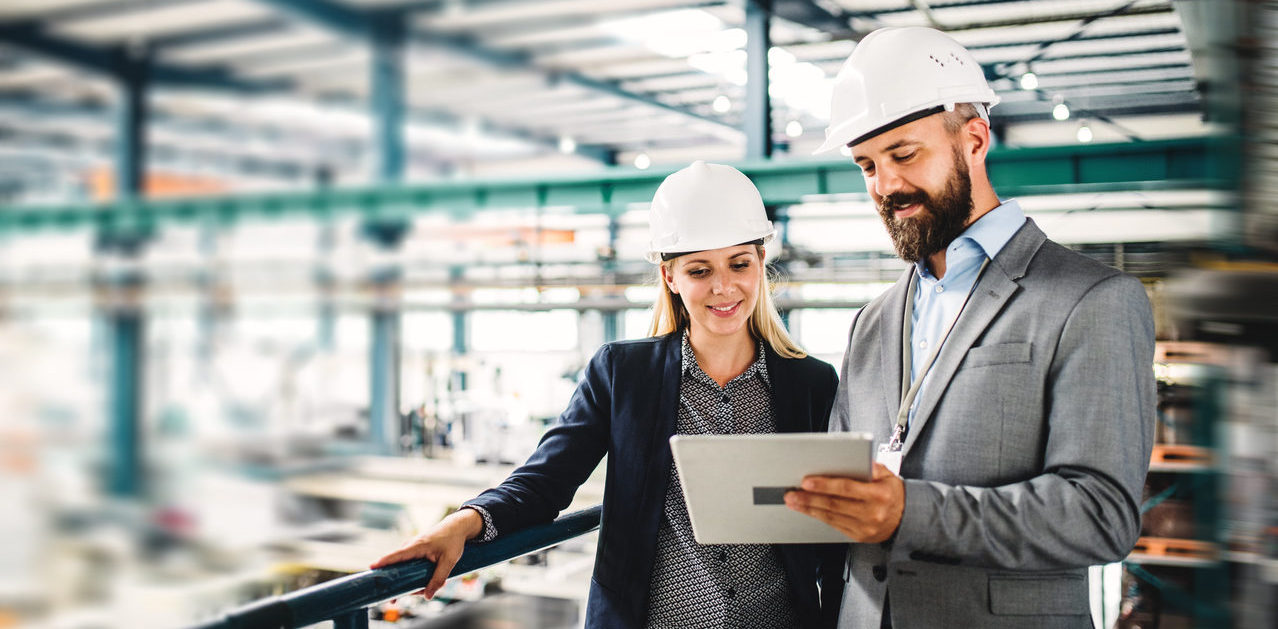
Insights
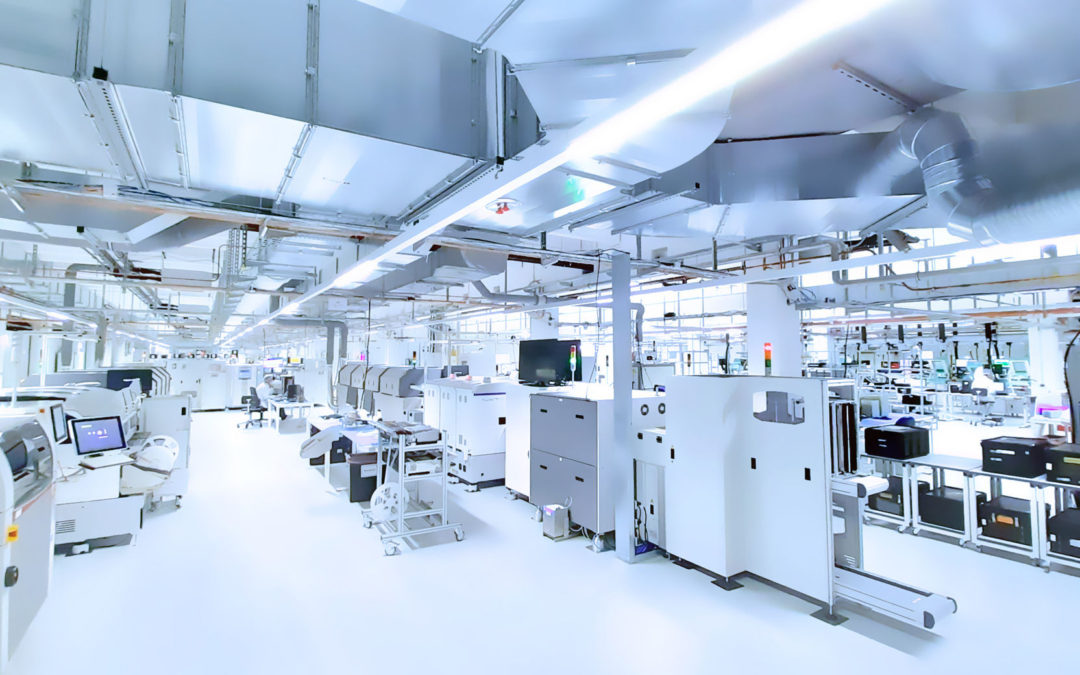
Fragile Supply Chains Bolstered By New Technologies
From the Covid-19 pandemic to the recent Suez canal blockage by the Ever Given container ship, events have exposed significant weaknesses in supply chains across the globe. Add Brexit trade tensions and the threat of various global tariff impositions into the mix, and conventional supply chains look decidedly fragile as we emerge from the pandemic.
When manufacturing ground to a near halt at the beginning of last year as the coronavirus rampaged across continents, gaps began appearing in supply chains spanning medical, automotive, aerospace, industrial goods, and many other industries, 3-D printing or Additive Manufacturing was able to plug some of the holes in supply chains where conventional manufacturing could not match demand.
“We have seen with the recent pandemic the vulnerabilities of the physical supply chain to systemic disruption,” says Quan Lac, Head of Additive Manufacturing at Siemens Energy, Americas. “There have been numerous examples of additive manufacturing being used to mitigate conventional supply shortfalls through digitally-enabled distributed manufacturing,” he adds.
According to the latest market research from industrial 3-D printing consultancy specialist AMPOWER, metal additive manufacturing could achieve annual growth of more than 29% over the next four years, despite a stagnation in the market due to the Covid-19 pandemic.
WTO, Siemens, Protolabs on how additive manufacturing bolsters global supply chain resilience
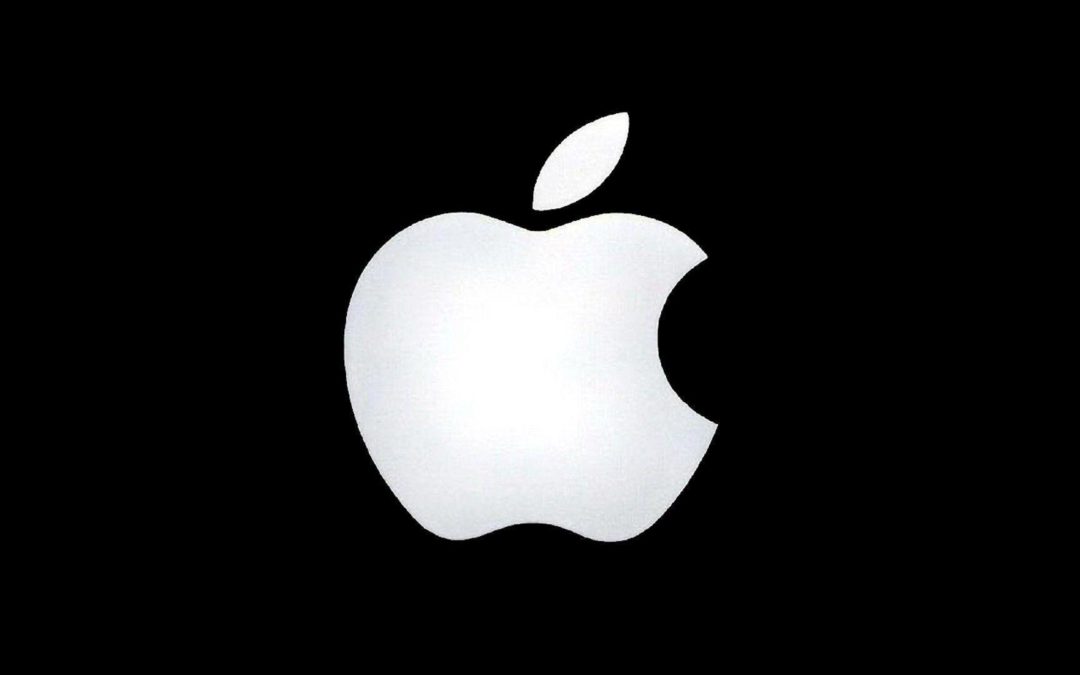
Apple Makes Huge Commitment to the USA
Apple has announced an acceleration of its US investments, with plans to make new contributions of more than $430 billion and add 20,000 new jobs across the country over the next five years. Over the past three years, Apple’s contributions in the US have significantly outpaced the company’s original five-year goal of $350 billion set in 2018.
Apple is now raising its level of commitment by 20 percent over the next five years, supporting American innovation and driving economic benefits in every state. This includes tens of billions of dollars for next-generation silicon development and 5G innovation across nine US states.
“At this moment of recovery and rebuilding, Apple is doubling down on our commitment to US innovation and manufacturing with a generational investment reaching communities across all 50 states,” said Tim Cook, Apple’s CEO. “We’re creating jobs in cutting-edge fields — from 5G to silicon engineering to artificial intelligence — investing in the next generation of innovative new businesses, and in all our work, building toward a greener and more equitable future.”
https://www.apple.com/newsroom/2021/04/apple-commits-430-billion-in-us-investments-over-five-years/
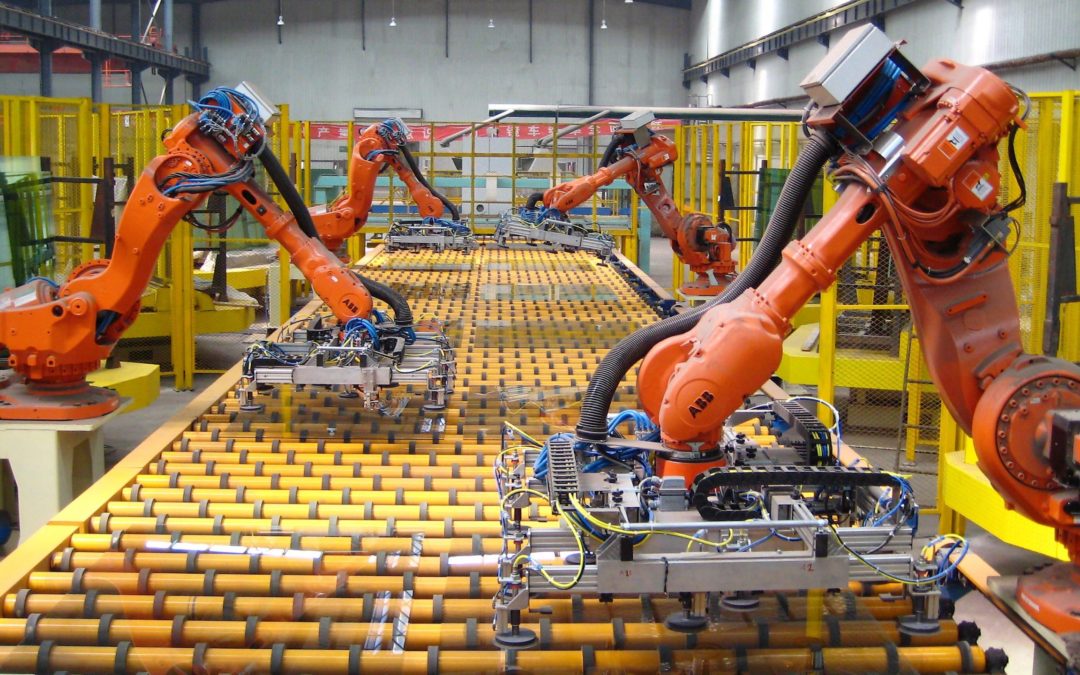
Manufacturing Shifting Back To The USA
Predictability, security, resilience, automation, ESG, and yes, lower overall costs favor the return to the USA of previously offshored manufacturing and supply chains.
Onshore or nearshore assembly, configuration and test is beginning to be deployed in several industries (large format industrial products, high tech equipment, and sectors where increased concerns for product security is a factor). This option has been under review and in motion by companies in many sectors where labor content as a percent of manufacturing cost has declined as a result of automation, where fuel costs are significant and have increased, and as import tariffs have become less predictable for their products. More recently, rising attention to carbon footprint impact and reliability of supply have added momentum to this movement.
The U.S. executive order promoting job creation and supply security in several technology areas like semiconductor and battery manufacturing is creating a further set of tax, landed cost and public sector sales considerations to those industrial companies using these technologies and with a large U.S. corporate presence and customer base.
Industrial product companies are thinking through and enacting several supply chain footprint scenarios including expanding regional manufacturing capacity within the USMCA and postponed final configuration within their U.S. based distribution network. In turn they are asking their suppliers and partners to adopt regional strategies that help shift country-of origin profile, lead time and landed cost across sets of products.
Reinvention of the landed cost equation and supporting supply chain structures is a predictability and trust priority. For some industrial product companies, landed cost now is going beyond part, manufacturing and freight costs to include cost predictability and total cost including import tariffs, costs associated with reactionary supply assurance and carbon offset costs. Likewise, lead time is increasingly focused on the total lead time of transforming raw material to a customer configured item even when volume is above forecast – not just the logistics lead time to get a finished item to a customer. Finally, supply chain quality is no longer just ‘the right product to the right place at the right time’ but is now including measures for excess and obsolete inventory, wasted capacity and stock-outs for many companies.
Security is another rising priority. The pandemic and tariff wars have pointed out that supply chains that are highly optimized for cost can have a latent and real high risk for reliability. Supply chain security is now being thought about in terms of data and intellectual property security, alternate sources of supply and routing are becoming a higher priority for supply chain management across more companies and industries.
Environmental, social, and governance (ESG) practices that promote value beyond revenue and profit are also resulting in a reversal of certain globalization trends. For example, the social component of ESG promotes diversity and inclusion in relation to how direct and indirect suppliers are selected. Suppliers providing services and products to a company now need to adopt their own ESG principles such as employment diversity and good employee management practices, in order to remain as suppliers.
All of these factors favor an acceleration of manufacturing and supply chains returning to North America.
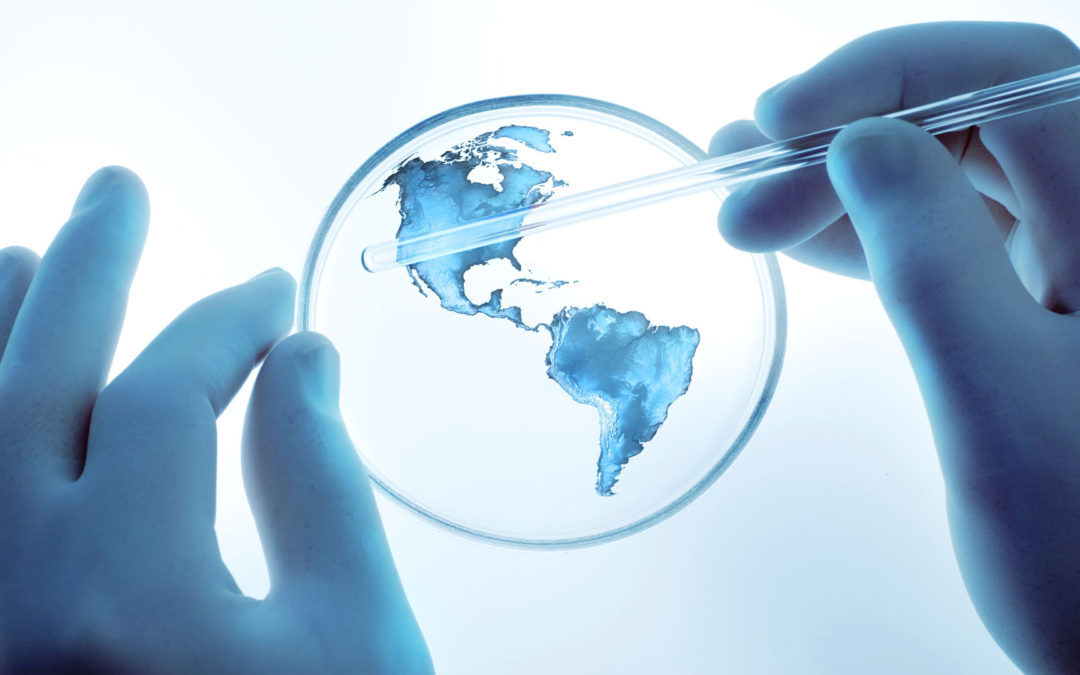
Returning Pharma Manufacturing To The U.S. Will Benefit Society
Pharmaceutical manufacturing is a strategic U.S. national asset that should never have been off-shored. Reliance on lower-cost manufacturing in Asia, particularly China, is a failed model that has been exposed by the pandemic. The supply chain review ordered by President Biden virtually guarantees that critical pharmaceutical manufacturing and supply chains will be returned to the U.S.
Even without a pandemic, dependence on distant pharmaceutical manufacturing and supply chains could be a huge problem if China were to halt exports of certain raw materials and the pharma ingredients used to produce important medicines as a retaliatory measure — in essence weaponizing life-saving treatments.
At the top of the list are antibiotics, which have been commoditized and offer little incentive for investment in innovation and new drug development. Others include common blood pressure medications and treatments for prevailing chronic diseases. The potential consequences are so acute that the U.S. Pentagon and top military officials were voicing the need for action back in the autumn of 2019. China has already started to restrict rare earths. How long before the same occurs with pharmaceuticals?
Imagine if the next pandemic was caused by a bacterium rather than a virus. Would China export any raw materials to other countries looking to produce antibiotics? Stockpiling antivirals and antibiotics is not an effective way to meet demand during a pandemic; it is only suitable for short-term requirements.
Manufacturing drugs in western countries while retaining high environmental standards, however, will drive innovations that will benefit future society. Local production capability is not required for every drug. The first step is to reshore manufacturing and supply chains for the top 100 medicines that treat the most common diseases.
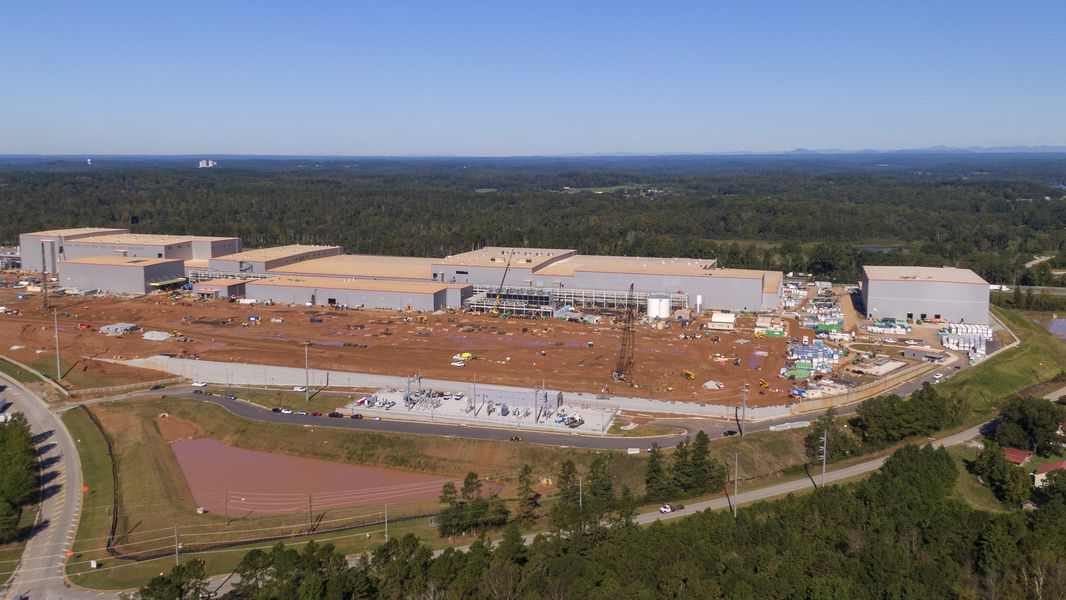
Georgia EV Battery Project Saved By Last Minute Deal
Two of the world’s largest EV battery manufacturers have reached a settlement that President Biden called “a win for American workers and the American auto industry.” The companies, SK Innovation and LG Chem, have been involved in a dispute after LG accused SK of misappropriating trade secrets. LG filed a complaint with the U.S. International Trade Commission in 2019 and the commission ruled in favor of LG, putting a 10-year ban on SK imports.
SK agreed to pay $1.8 billion in cash and royalties to LG in the settlement, and both South Korea-based companies agreed not to sue each other for the next 10 years. The settlement means SK can finish building an EV lithium-ion battery plant in Commerce, GA., which will provide batteries to Ford and Volkswagen.
The deal came just hours before a deadline in which Biden would have needed to decide to overrule the ITC or to let the ruling stand and potentially lose jobs and resources that would help him reach his electric vehicle goals for the U.S. Within Biden’s $2 trillion infrastructure plan is $174 billion set aside for increasing EV sales and production.
“We need a strong, diversified and resilient U.S.-based electric vehicle battery supply chain, so we can supply the growing global demand for these vehicles and components – creating good-paying jobs here at home, and laying the groundwork for the jobs of tomorrow,” Biden said in a statement about the announcement.
Contact Us
