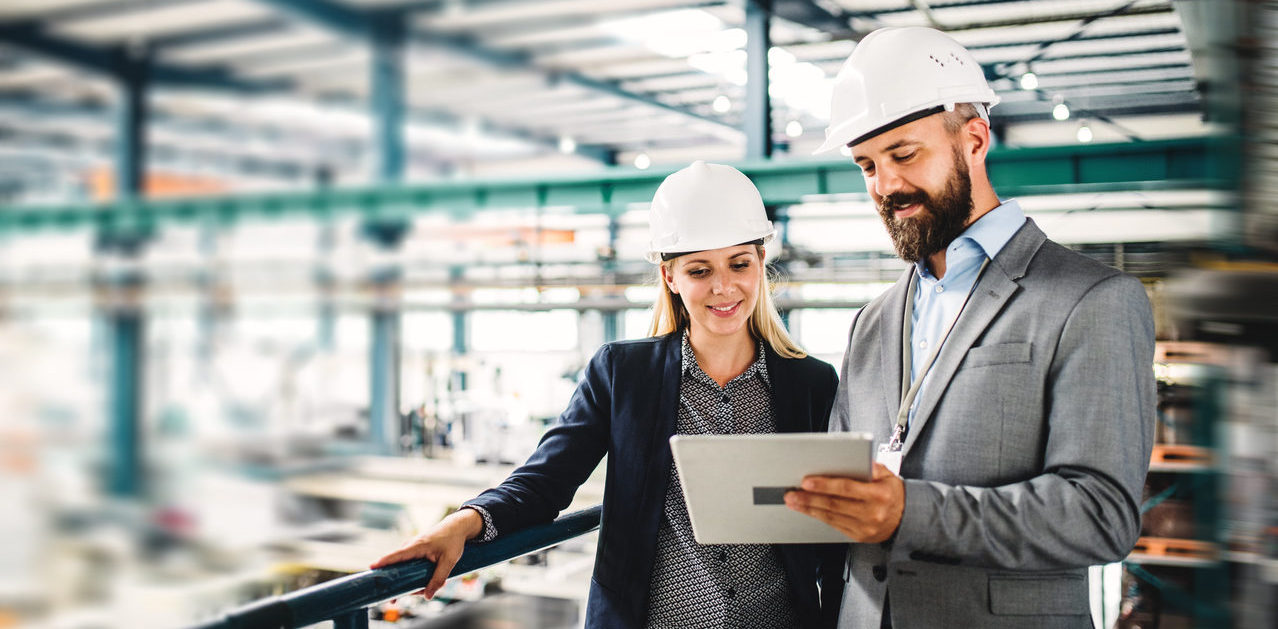
Insights
‘Slowbalization’ Is Helping the U.S. to Grab Next-Gen Supply Chain Opportunities
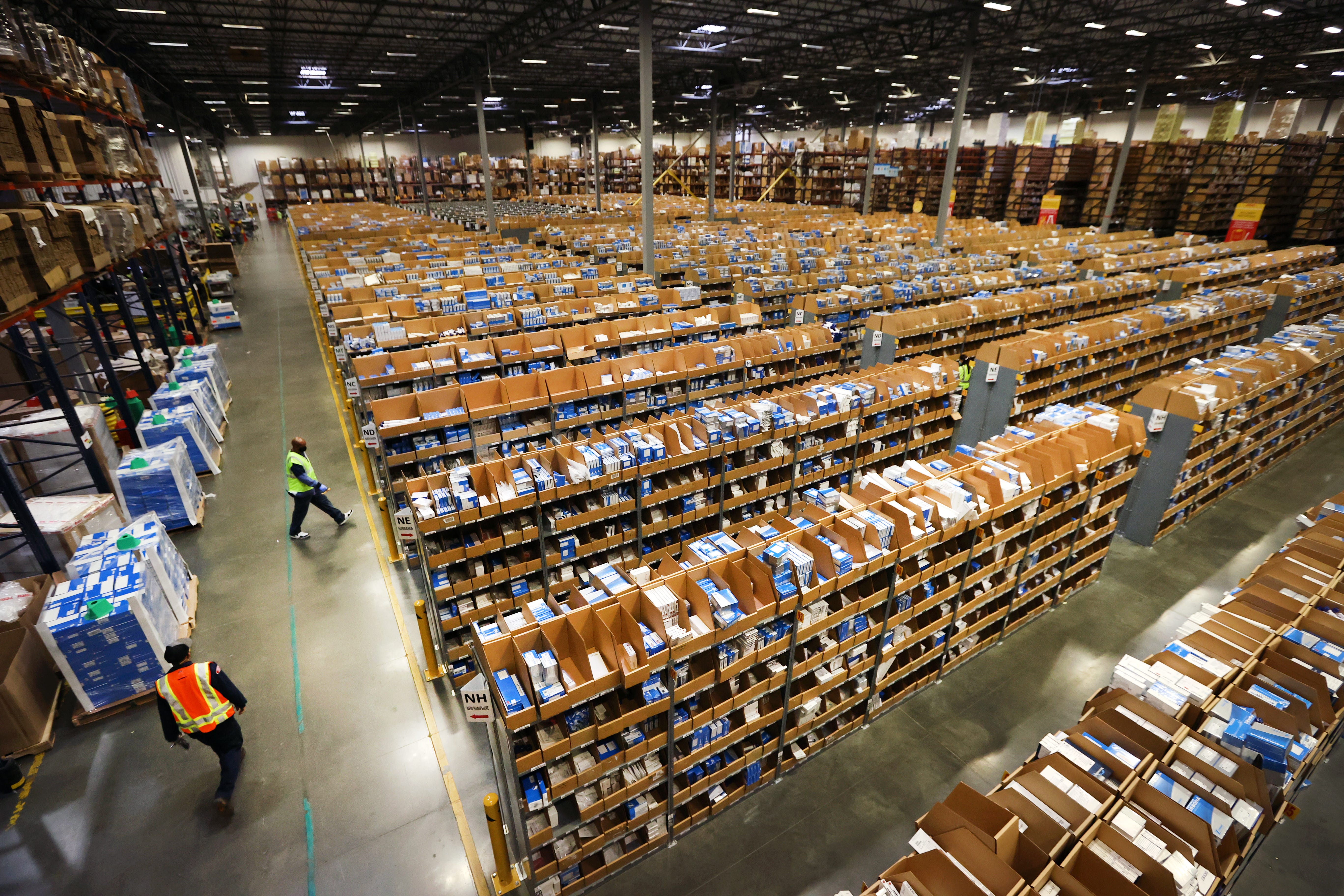
Starting in the 1990’s and accelerating after the inclusion of China in the World Trade Organization in 2001, many companies globalized (offshored) their sourcing and production and embraced lean manufacturing techniques to reduce costs. Globalization has evolved into ‘slowbalization’ due to many unforeseen risks. Offshoring exposed companies to a plethora of supply chain risks, such as extreme weather events, labor disputes, cyberattacks, and supplier disruptions. COVID-19 is not the first epidemic to disrupt supply chains—SARS, measles, swine flu, Ebola, and avian flu all resulted in business interruptions—but none of these epidemics disrupted global trade and domestic supply chains as much as COVID-19.
The leading multinationals have long recognized that managing supply chain risks is necessary for their sustained competitiveness. President-elect Joe Biden has announced a plan to rebuild U.S. supply chains that aims for broad-based resilience as opposed to pure self-sufficiency. Additionally, there have been multiple Senate hearings to examine the integrity and reliability of critical supply chains following the onset of the pandemic.
One potential way to improve supply chains involves public-private partnerships. The SecureAmerica Institute at Texas A&M University is one such a partnership, made up of a network of about 100 partners across several technical domains within the manufacturing base. The program employs a novel interdisciplinary paradigm to build on policy, economics, and supply chain management research and education. https://www.brookings.edu/techstream/how-to-build-more-secure-resilient-next-gen-u-s-supply-chains/
New Mexico Lures Taiwanese Companies Through Strong Mexico Connection

Reshoring efforts have successfully attracted three Asian companies (Cymmetrik, Xxentria and Admiral Cable) to Santa Teresa, NM, bringing 400 new jobs. The U.S. government and many local entities have been pushing for relocation of manufacturing facilities from Asia after disruptions in the supply chain caused by the COVID-19 pandemic.
Santa Teresa promoters and New Mexico officials have moved aggressively in the past few months to pitch competitive production costs across the border in Mexico, as well as the growing port of entry, rail connections in Santa Teresa, and recent completion of a multimillion dollar renovation at The Doña Ana County International Jetport in Santa Teresa that has increased cargo handling capacity. https://www.borderreport.com/hot-topics/trade/new-mexico-lures-taiwanese-companies-through-strong-mexico-connection/
The Pandemic Has Severely Harmed Global Supply Chains

The coronavirus pandemic has left some of the world’s biggest shipping lines facing mounting backlogs and delays, straining international supply chains and disrupting global trade. Operators say the container shipping industry — the backbone of global trade — is under severe pressure due to the combined impact of staff illness, quarantining and social distancing, along with soaring consumer demand and disruption to factory output caused by lockdowns. Lars Jensen, chief planner of services for Maersk Line, the world’s biggest container ship operator, said there was a “perfect storm” created by a mix of rising demand and reduced capacity in logistics systems.
These issues have caused many shippers to reevaluate their supply chain risks and begin a shift toward more localized models, where production is located closer to customers.
https://www.ft.com/content/eb21056b-5773-422a-ab78-92e59cddc1b5
Smart Manufacturing Is The Secret To A Stronger Economy

Gartner estimates that AI augmentation could generate $2.9 trillion of business value in 2021. Smart manufacturing will boost the economy and enable manufacturers to meet the modern needs of factories, supply chains, and customers. With more sensors, networks, and data monitoring and recording every step of the process than ever before, U.S. manufacturing is getting smarter thanks to digital technology. Autonomous systems detect and respond to problems, enabling the adaptation of machinery and systems to changing conditions, and the deployment of artificial intelligence further allows manufacturers to optimize every aspect of the value chain. All of these processes are accelerating innovation and product development, while dramatically reducing costs and risks.
Neural Manufacturing Is the Future
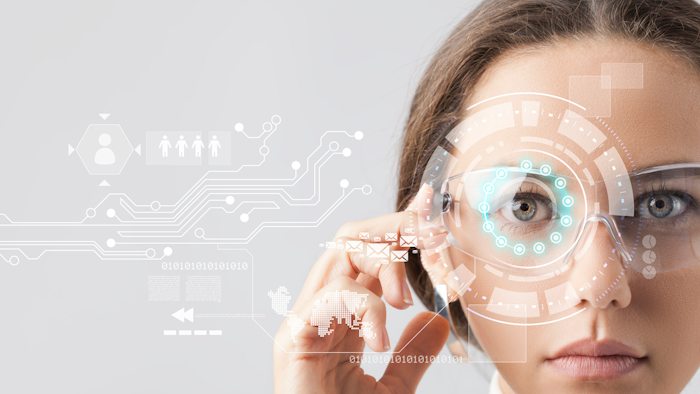
Neural Manufacturing will become widely-adopted as companies seek ways to improve efficiencies and reduce costs. Neural Manufacturing is a smart process that incorporates digital technology into many aspects of the manufacturing process to assess and predict problems and proactively course-correct with real-time solutions. This approach has saved time and money for companies integrating automation with human workforces. Neural Manufacturing can reduce the number of steps in the manufacturing process and better calibrate the quantity of components and raw materials needed in inventory. Neural Manufacturing can also fine tune logistics and improve supply chains by pre-scheduling shipping to coincide with production schedules.
Contact Us
