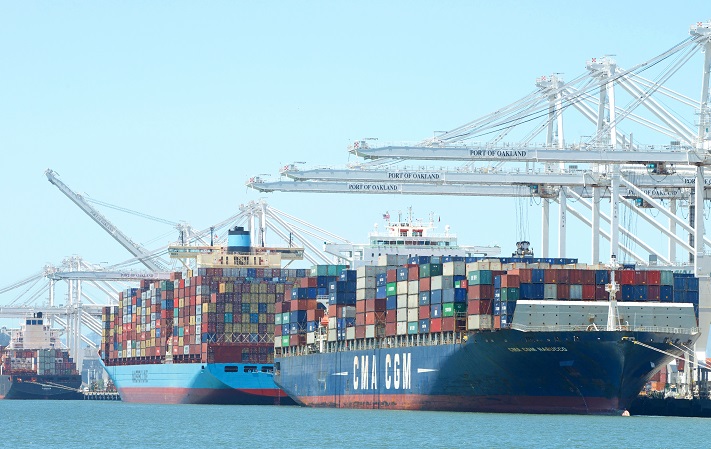
The pandemic and other factors have disrupted international trade, causing massive delays and shipping container shortages that have substantially increased the cost of shipping goods. This dynamic is adding fresh momentum to the trend of reshoring and localizing of production/supply chains. At the center of this storm is the international shipping container, the workhorse of globalization that could have a fate similar to the dinasaurs if localization takes hold.
Off the coast of Los Angeles, more than two dozen container ships filled with exercise bikes, electronics and other highly sought imports have been idling for as long as two weeks. In Kansas City, farmers are struggling to ship soybeans to buyers in Asia. In China, furniture destined for North America piles up on factory floors.
“I’ve never seen anything like this,” said Lars Mikael Jensen, head of Global Ocean Network at A.P. Moller-Maersk, the world’s largest shipping company. “All the links in the supply chain are stretched. The ships, the trucks, the warehouses.” Peter Baum’s company in New York, Baum-Essex, uses factories in China and Southeast Asia to make umbrellas for Costco, cotton bags for Walmart and ceramics for Bed Bath & Beyond. Six months ago, he was paying about $2,500 to ship a 40-foot container to California. “We just paid $67,000,” he said. “This is the highest freight rate that I have seen in 45 years in the business.”
https://www.nytimes.com/2021/03/06/business/global-shipping.html